Get an inside-look at the Taylor Guitars factory in sunny San Diego as the PMTVUK Crew head to the USA in search of the latest and greatest guitar gear
Words by Meg Linford
As an acoustic guitarist and musician - and one who is also the proud owner of a beautiful Taylor acoustic - it may come as no surprise to you that visiting the Taylor factory back in March was one of my favourite days ever. Based down in sunny San Diego, they have an amazing complex of buildings and factories that we had the absolute pleasure of spending the day exploring.
We drove down from North Los Angeles to San Diego the night before, ready to be up early in the morning to find the location. When I say this was like Christmas Eve for me, I don’t say it lightly. Having been a huge fan of Taylor Acoustics for a long time I knew this day was going to be inspiring, and I couldn’t wait to get stuck into the content.
Arriving bright and early in the morning, we were greeted by Chris and Zach who led us through the visitors reception and got us ready for the tour. The first thing we were taken aback by was just how big the campus is! In fact, we spotted people whizzing around between buildings on golf buggies, just so they didn’t have to walk the long walks between buildings. The vast scale of the operation was really impressive and we had a whole day planned which would allow us to move between a few of these different buildings. How exciting!
We started off the day with the legend himself, Mr Andy Powers, (who I still can’t believe we had the pleasure of meeting). We got a peek into his new workshop, fitted with secret design sketches on the walls, beautiful wooden furniture, and a giant rustic wood worktop in the centre. Just as we expected, Andy was an absolute joy to speak to.
Before we’d even turned the camera on he shared with us some amazing stories of how he began his journey making guitars and gave us a little sneak peek at some new models. Once we got rolling with the interview, it was truly a sermon on all things acoustic guitars. Andy's story of how he began creating guitars around the age of 8, using bits of old wood in his Dad's wood workshop was mind blowing.
By the age of 12 he had a waiting list of musicians who wanted one of his home built guitars! He worked on this all the way up to finishing school, and by the time he began work with Bob Taylor he told us of the backlog of guitars he had waiting to be made. We then delved into some of his most exciting projects when he began work at Taylor. Andy mentioned the revamping of the amazing 800 series guitars, and if you haven’t had the chance of trying one of these before, I can assure you that they are some of the most beautiful and rich sounding acoustics I've ever played.
We also touched on the revolutionary V-Class bracing which Andy designed to bring a whole new layer of tonal qualities and resonance to Taylor guitars. Unlike the standard X-style bracing, the V-Class bracing really helps aid volume and resonance in a whole new way.
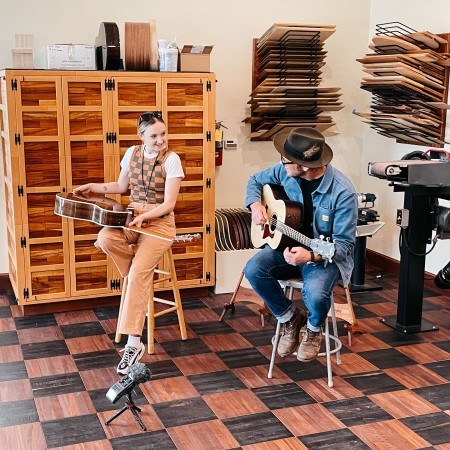
One thing that has always impressed me about Taylor guitars is their push for sustainability, and it was great to hear about their current and future projects for keeping this at the forefront of their designs. We discussed how Taylor began sourcing woods from local areas of California during the 2020 lockdowns as they noticed different types of trees in the California area which were being removed each year for various reasons and would then be ground up.
Through trial and error they managed to discover that Ash from California makes for a great sounding tonewood with some unique qualities. This is now a wood that is a big part of the new GT series of guitars and I am so impressed with how great it sounds. Sourcing wood from the local area is a great way to keep sustainability at the forefront in your practice.
Getting to have this chat with Andy was incredibly inspiring and really felt like such a privilege to delve into the psyche of a master builder and an all round master in guitar! Our day continued with a fantastic chat with Rob Magargal who heads up the Taylor repairs and services side. Rob was playing guitar as we walked in, explaining to us how he is left handed but has mastered the art of playing the right handed guitar - left handed!
We were already off to a great start. I spend a lot of my time working in the PMT stores and working on acoustic guitar repairs, so this chat with Rob was packed full of valuable and super-useful information for anyone out there with an acoustic guitar. We discussed how important it is to look after your Taylor, from making sure the humidity of the room is kept at an ideal, to where to store your guitar for optimal playability. The recommended humidity for your guitar he told us is 44-50% humidity and we discussed some of the ways you can best manage this at home if you don’t have yourself a fancy dehumidifier. Some of these great suggestions included a hygrometer, an easily portable and small humidity level reader which you can leave with your guitar in its case to find out the conditions.
On the subject of guitar cases, this was another top tip to help with keeping your guitar in the best condition possible - to leave it in your hard case or well-padded bag. This will just help give you that extra layer of protection against the outside conditions.
Rob had just hit his 31-year anniversary working for Taylor, and it was a joy to hear him talk about his job with such excitement and passion even after all those years! Next up in our day, a tour of the Factory with another long standing Taylor Guitars employee and appointed ‘Taylor Historian’, Jim Kirlin.
When you think of a guitar factory you think of a big operation, with machines and lots of people working on parts. Well this factory is that and more! We were completely blown away by the sheer size of the whole place - each department had its own working space, from woods, to paint, to the final stages of stringing and tuning the instruments. Every space was quite spectacular. Jim led us around the place, starting in the huge ‘woods’ room, full of every species of tonewood you can imagine.
The process from getting the woods into the factory to selecting which tonewoods are used for each model is just as intricate as you’d imagine. Drying the woods before they can even be used takes months! Going through the wood acclimating area, we were able to see the amazing laser machines at work, shaping the different tone woods into body shapes. As we moved through the factory we then got to see the guitars at each different stage of their journey, from how the bracing is made to eventually joining the tops, back and sides together. What a process. Then from there it was over to the buffing machines.
We watched in awe as the mechanical arm picked up the body and moved it over to be buffed. Surrounding us were racks and racks of finished buffed bodies of all different models looking shiny and ready for the next part of the assembly process. Another unique thing about Taylor is that they build a lot of their own tools and parts for their computer mills in-house - this makes the whole process feel even more home-grown.
Jim then talked us through the process of their UV oven and how they moved over from hand-spraying nitrocellulose lacquer to a UV finish, which is more environmentally-friendly and also shortens the process and curing time. The more intricate parts of the build were the last places we visited, where we got to see the assembly of the neck joint to the body, then how they assemble the tuning heads to the headstock, and lastly finishing with the team who look after stringing, tuning, and setting-up the guitars. The whole team of employees we met across the factory were friendly and very open to sharing their work with us. I was completely blown away by each part of the tour (and I know you all will be too).
A part of Taylor that maybe isn’t thought of as much as their guitars is their Taylorwear product range. This includes everything accessories - from plectrums and guitar straps, all the way up to humidifiers. Dave kindly talked us through the entire range and there were even some products there that I hadn’t seen yet in the UK! Taylor makes a great selection of capos, made from a range of different resources, as well as straps, even some vegan straps for those looking for a great quality, non-leather strap. The humidifier pack available would be a great solution to the issues I mentioned earlier on that we discussed with Rob, and Dave showed us just how simple and easy to use this is. By leaving it in your guitar case you can consistently keep track of the conditions of your guitar. A game changer!
The thing that stood out for me the most in this chat was the thoroughness and thought that has gone into the Taylor plectrum range. Now if you are anything like me, you use the plectrum that feels the most comfortable, tend to always use that one and never really consider the different tonal qualities that each pick might open up. Well, the demonstration from Dave where he went through each of the different plectrums really changed my mind on this. Every plectrum is made from a different material, some from wood, some from nylon, and all with different thicknesses. Every single one really did have a different tone it brought out in the guitar, and it was so noticeable I can't believe I hadn’t considered it before. I am certainly taking this into consideration now when choosing which one of their plectrums to use on-stage at my shows.
Dave and Zach, our aforementioned trusty tour guide, then ended the day nicely by talking us through some of the latest models that Taylor had coming out. This was a great way to end our tour, getting to play each model and talk through the distinct differences between them. It was so interesting to hear the thought processes behind why Bob Taylor and Andy Powers have designed each new model the way they have and get to hear a sneak preview of how they all sound. All I will say is that there are some seriously beautiful guitars due out very very soon. So definitely keep your eyes peeled!
So that rounds off our day at the Taylor Guitars factory in San Diego. I’m incredibly grateful to have been given the opportunity to see the factory, hear about the history, see the process of the builds and be given a deeper insight into the ethos and brand that is Taylor. Everyone we spoke to was brilliant and I came away with a head full of fantastic and insightful knowledge. If I wasn’t already a huge Taylor fan, I am even more of one now.